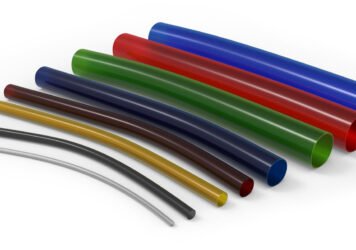
3D Printing vs. Extrusion: What are the Differences?
In the world of plastics and manufacturing, both 3D printing and extrusion play vital roles, but they serve very different purposes and operate through distinct processes. Understanding these differences can help businesses choose the right technology for their product needs, whether it’s rapid prototyping or large-scale production of plastic components.
Let’s take a detailed look at how 3D printing and extrusion compare.
What Is Plastic Extrusion?
Plastic extrusion is a manufacturing process used to create continuous lengths of plastic profiles, tubes, sheets, or custom shapes. The process involves melting plastic pellets and forcing the molten material through a shaped die to form the desired cross-section. Once extruded, the plastic is cooled and cut to length. Extrusion is ideal for producing large quantities of uniform parts efficiently and cost-effectively.
What Is 3D Printing?
3D printing, or additive manufacturing, builds objects layer by layer from a digital 3D model. There are several types of 3D printing technologies, but many common methods use plastic filament or resin that is selectively deposited or cured to create a final part. Unlike extrusion, which creates continuous profiles, 3D printing is often used to produce complex, customized, or one-off parts with intricate geometries.
Key Differences Between 3D Printing and Extrusion
Process and Production Scale
- Extrusion is a continuous process designed for high-volume manufacturing. It excels in producing long, consistent profiles like tubing, rods, or weather stripping with tight tolerances and repeatability.
- 3D Printing is an additive, layer-by-layer process optimized for low-volume runs, prototyping, or custom parts. It allows for on-demand production without the need for tooling or dies.
Material Use and Properties
- Extrusion typically uses thermoplastic pellets that are melted and shaped. The material properties are consistent because of the controlled process, making extrusion suitable for structural or functional parts.
- 3D printing can use a broader variety of materials, including specialized filaments or resins. However, parts may have different mechanical properties depending on printing orientation and layer adhesion, which can affect strength and durability.
Design Flexibility
- Extrusion is limited to creating parts with a uniform cross-section along their length. Complex 3D shapes are not feasible through extrusion alone.
- 3D printing offers unmatched design freedom, allowing the creation of intricate geometries, internal cavities, and complex assemblies without additional manufacturing steps.
Speed and Cost
- For large production runs, extrusion is much faster and more cost-effective per unit once the tooling is in place. The initial cost of dies and setup can be high, but unit costs drop significantly at scale.
- 3D printing has minimal setup costs, making it economical for prototypes or small batches. However, it can be slower and more expensive per part in mass production scenarios.
Applications
- Extrusion is commonly used for producing items like plastic tubing, window profiles, pipes, seals, and various industrial components where uniformity and strength are crucial.
- 3D printing shines in rapid prototyping, custom medical devices, small batch manufacturing, and complex parts that would be difficult or impossible to create with traditional methods.
Choosing the Right Technology
For companies needing large volumes of consistent plastic profiles or parts, extrusion is usually the best choice due to its efficiency and cost-effectiveness. Meanwhile, 3D printing is ideal when flexibility, customization, and quick turnaround are priorities.
Many manufacturers today integrate both technologies into their processes—using 3D printing for early-stage prototyping and extrusion for full-scale production—maximizing the benefits of each.
Custom Extrusion with Inplex
Looking for quality custom extrusion products and services? Inplex is one of the leading custom extrusion services in the US and has almost 60 years of experience. We pride ourselves on our ability to put the right talent and technology in place to perform the best possible job for our clients.
We own a 42,000 sq. ft. facility in Naperville, Illinois, that is temperature-controlled and features an environmentally friendly closed-loop water cooling system. If you have specific needs or questions, don’t hesitate to contact us!
Back to Blog