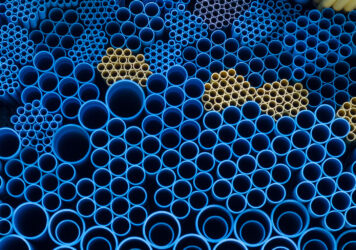
A Guide to Material Selection for Extrusion
Choosing the right material is one of the most critical steps in the plastic extrusion process. We know that material selection impacts everything — from performance and durability to production efficiency and final product appearance.
Whether you’re designing a custom profile for construction, refrigeration, lighting, or industrial use, understanding your material options ensures a successful outcome. Here’s a guide to help navigate the selection process. Let’s take a closer look.
Key Factors to Consider
Application Requirements
Start by identifying the specific requirements of your application. Will the plastic part need to withstand extreme temperatures, UV exposure, chemical contact, or physical impact? For instance, profiles used outdoors often require UV-resistant materials like acrylic or specially formulated PVC, while industrial equipment components may demand high-impact ABS or polycarbonate.
Mechanical Properties
Each material offers a unique set of mechanical characteristics, such as flexibility, hardness, tensile strength, and impact resistance. If flexibility is needed, materials like polyethylene (PE) or thermoplastic elastomers (TPE) are strong choices. For more rigid and structural applications, polystyrene (PS) or rigid PVC might be more appropriate.
Environmental Conditions
Environmental exposure plays a big role in material selection. Plastics intended for outdoor use must resist weathering, while parts used in cold environments, like refrigeration seals, require materials that remain flexible at low temperatures. We often recommend materials like silicone or specially modified PVC blends for cold applications.
Aesthetic and Finish Requirements
Color, gloss, and surface texture are often as important as performance. Some projects require custom color matching, while others prioritize clarity or matte finishes. Materials like acrylic (PMMA) provide excellent clarity for lighting applications, while PVC can be easily color-matched and textured.
Regulatory and Compliance Needs
Some industries, such as medical, food service, and construction, have strict regulatory standards. It’s important to choose materials that meet FDA, UL, NSF, or other certifications if needed. Inplex helps customers select compliant materials to meet industry-specific regulations without compromising design or functionality.
Common Materials for Plastic Extrusion
- PVC (Polyvinyl Chloride). Highly versatile, cost-effective, available in rigid and flexible grades. Great for construction and industrial profiles.
- ABS (Acrylonitrile Butadiene Styrene). Strong, impact-resistant, and ideal for structural components.
- Polycarbonate (PC). Offers excellent strength and optical clarity; ideal for demanding applications.
- Polyethylene (PE). Flexible and chemical-resistant; commonly used for tubing and protective profiles.
- Polystyrene (PS). Lightweight and easy to process; used in displays and lightweight structures.
Custom Extrusion with Inplex
Looking for quality custom extrusion products and services? Inplex is one of the leading custom extrusion services in the US and has almost 60 years of experience. We pride ourselves on our ability to put the right talent and technology in place to perform the best possible job for our clients.
We own a 42,000 sq. ft. facility in Naperville, Illinois, that is temperature-controlled and features an environmentally friendly closed-loop water cooling system. If you have specific needs or questions, don’t hesitate to contact us!
Back to Blog