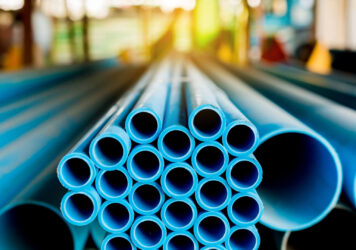
An Inside Look at the Plastic Extrusion Process: From Concept to Completion
From concept to completion, custom plastic extrusion is a collaborative and precise process that combines engineering, material science, and manufacturing expertise to deliver high-quality, application-specific solutions. Custom plastic extrusion is a versatile manufacturing process that transforms raw plastic materials into specific shapes and profiles.
The process progresses systematically from concept to completion, ensuring that the final product meets the desired specifications. Let’s take a general look at how the process works.
Concept and Design
Understanding Requirements
The process begins with a clear understanding of the application and performance requirements, including:
- Shape, size, and dimensions.
- Material properties (e.g., flexibility, durability, UV resistance).
- Aesthetic and functional features.
Design and Prototyping
- CAD Design: Engineers create detailed designs and technical drawings of the extrusion profile.
- Prototype Development: A prototype may be produced using 3D printing or similar technologies to validate the design.
Material Selection
The choice of plastic depends on the intended use. Common materials include:
- PVC: Versatile and cost-effective.
- Polycarbonate: Strong and transparent.
- Acrylic: Durable and visually appealing.
- Polyethylene/Polypropylene: Lightweight and chemical-resistant.
Additives, such as colorants, UV stabilizers, or fire retardants, are selected to enhance performance.
Tooling and Die Creation
Custom Die Design
A die is a metal tool that determines the shape of the extrusion. It is precision-engineered to match the design specifications.
Die Fabrication
Using CNC machining or EDM (electrical discharge machining), the die is created and tested for accuracy.
Extrusion Process
Material Preparation
- Plastic pellets or resins are mixed with any necessary additives.
- The material is dried to remove moisture, preventing defects during extrusion.
Extrusion
- Melting: The plastic material is fed into a heated barrel where it is melted by friction and heat.
- Shaping: The molten plastic is pushed through the custom die to form the desired profile.
- Cooling: The extruded plastic is immediately cooled using water baths or air chambers to solidify its shape.
Post-Processing
- Cutting and Sizing: The extruded profile is cut to the required lengths.
- Finishing: Processes such as trimming, drilling, or surface texturing are applied if needed.
- Quality Control: Products undergo inspections to ensure they meet tolerances and quality standards.
Custom Extrusion with Inplex
Looking for quality custom extrusion products and services? Inplex is one of the leading custom extrusion services in the US, with over 50 years of experience. We pride ourselves on our ability to put the right talent and technology in place to perform the best possible job for our clients.
We own a 42,000 sq. ft. facility in Naperville, Illinois, that is temperature-controlled and features an environmentally friendly closed-loop water cooling system. If you have specific needs or questions, don’t hesitate to contact us!
Back to Blog