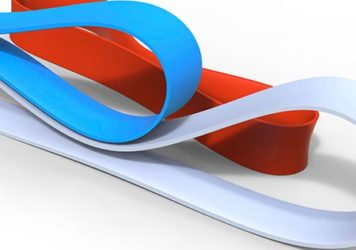
Custom Plastic Profiles: Extrude Your Version of Perfection
Custom plastic profile extrusion is the process of melting down plastic material and forcing it through a die in order to mold it into a desired shape and profile. The resulting product is then mechanically cut and finished to fit each specific order, with a wide variety of sizes, shapes, and colors available. Extruded products are vital in our day-to-day lives and are ubiquitous in medical equipment, electrical utilities, toys, consumer housewares, and various highway safety products. Such a variety of products and uses corresponds to the wide array of compatible materials and flexibility that the extrusion process affords in creating custom profiles to meet your exact specifications.
The plastic profiles created in the extrusion process can be either flexible or rigid. Both offer advantages for different use cases. Furthermore, the translucence of plastic extrusions can fall anywhere on a sliding scale from transparent to opaque – depending on the desired outcome and look of the material at the end of the extrusion process.
Types of Custom Profiles
Flexible
Flexible profiles are constructed with materials like polyurethane, Santoprene, and flexible vinyl (FPVC). These flexible materials can also be co-extruded to allow for a novel combination of colors and material types. Flexible plastic profiles are often used to make connecting sections or seals for doors, curtain walls, and expansion joints.
Rigid
As the name suggests, rigid plastic profiles tend to be harder and more inflexible. As a result, rigid plastics are naturally suited for external environments, where they can serve as a cost-effective and durable alternative to metal products. Materials used for rigid plastic extrusion include ABS, rigid vinyl (RPVC), high impact polystyrene (HIPS), polycarbonate, butyrate, propionate, and PETG.
Translucence
It is possible for skilled extruders to produce final objects of varying degrees of translucency, from transparent to completely opaque and anything in between. This ensures that the extruded material will come out exactly as you need it. For instance, it is possible to have custom plastic tubing produced to your exact color and opacity specifications.
Flexible Profiles
Polyurethane
Polyurethane is distinguished by its excellent resistance to wear. It packs a good deal of flexibility as well and can be molded in a variety of shapes and colors for use in different environments. Polyurethane tubing comes in two major types, namely polyester-based and polyether-based. Polyester-based polyurethane tubing offers particularly strong resistance to fuels and oils, while polyether-based tubing is best used in applications dealing with water or humidity. Products made from polyurethane are pervasive, from insulation to surfboards to car airbags and much more. This material also serves as a spill- and scratch-resistant protective floor coating on a wide range of floors, including wood and cement.
Santoprene
Santoprene thermoplastic vulcanizate (TPV) was originally created to serve as a material for molding tires. While it ultimately never succeeded at its intended purpose, it nonetheless found regular use in the automotive sector in other ways, thanks to its high fluid resistance and excellent sealing performance. Automotive parts commonly made from Santoprene include weather seals, bumpers, cable jacketing, and much more. Santoprene TPV’s superior sealing property also makes it especially useful in construction, where it can be used to make window seals, tubing, electrical connectors, and caster wheels. The medical industry has also found notable use for Santoprene as a gasket on syringe plungers.
Flexible Vinyl (FPVC)
Commonly regarded as one of the most versatile and cost-effective materials, PVC can be made very soft through the extrusion process with the use of a plasticizer or other additive. Due to its strong insulation properties and abrasion resistance, flexible PVC is commonly used for plastic profile extrusion. As a recyclable thermoplastic, flexible vinyl also provides exceptional environmental performance. The flexibility inherent in FPVC comes with a drawback, however, in that it is not able to tolerate as much pressure as rigid vinyl (RPVC) and is more prone to kinking at lower densities. FPVC is especially useful for plastic packaging, as its flexibility allows it to be formed into unconventional shapes such as jar lids. It has also found use in home construction, especially in flooring, roofing, and wall covering. While FPVC has been noted for being able to serve as packaging material to carry a wide range of substances, it can also be ordered according to FDA standards for applications involving food or drinking water.
Rigid Profiles
ABS
Acrylonitrile butadiene styrene (ABS for short) is a rigid yet lightweight thermoplastic polymer. It enjoys strong resistance to physical or chemical damage and is impervious to rotting and corrosion. Combined with its relative inexpensiveness, it is no surprise that ABS sees major use in a variety of applications. Some items commonly made from ABS are golf clubs, toys, keyboards, automotive parts, and musical instruments. ABS can also be found in a variety of household items such as wall sockets, cameras, and cases for power tools.
Rigid Vinyl (RPVC)
Unsurprisingly, rigid vinyl (RPVC) finds its most effective use when rigidity is particularly desired. RPVC combines excellent resistance properties to water and chemicals with affordability, making it a popular choice in tubing and profiles. However, given that PVC contains chemical additives like lead and cadmium, it must be ordered at FDA grade to be safe to use for applications involving drinking water.
RPVC is used most commonly in plumbing and the construction industry in general. It can be extruded into many different colors and offers versatility for outdoor projects.
High-Impact Polystyrene (HIPS)
High-impact polystyrene (HIPS) was first discovered in the 1930s when rubber was added to basic polystyrene. As a result, HIPS has much-improved durability and strength, causing it to be used widely in packaging. Its stiff, low-strength form has found applications in toys, point of purchase displays, plastic cups, and automotive parts.
Polycarbonate
Known for its flexibility and temperature resistance, polycarbonate is one of the most common materials used in extruding. It can be shaped into virtually any form through repeated cooling and reheating and serves as an excellent insulator. Polycarbonate can be found in aircraft components, eye protection, and media discs like CDs and DVDs. While polycarbonate is susceptible to scratching, it is possible to apply anti-scratch coating and order it in any available color.
Butyrate / Propionate
Butyrate and propionate are synthetic thermoplastics that bear a high capacity for light reflection, making them clear materials. As a result, they are particularly useful in lighting and general outdoor applications. While their heat resistance is lower than that of polycarbonate, butyrate and propionate sport excellent liquid absorption and impact strength properties. Common manufacturing applications include pen barrels, eyeglass frames, toys, and toothbrush handles. They may also be used for tubing and profile applications.
PETG
Polyethylene terephthalate glycol (PETG) is an FDA-certified thermoplastic material that is known for its strength and durability. Light and pliable, PETG also sports impressive impact resistance and features high light transparency. The most notable drawback of PETG is its lack of UV resistance, which means that it may melt or warp if left out in the sun for extended periods of time. Being more cost-effective than polycarbonate, PETG is used for a wide variety of applications. These include medical implants and devices, robotics and electronics, and in storefronts.
The extrusion process can make use of a variety of materials, from rigid to flexible, to manufacture custom plastic profiles to meet exacting specifications. The key is to know which polymer material matches your needs most closely in terms of both its chemical properties and its relative cost-effectiveness. While the material you end up working with will largely depend upon the intended industrial application of the final product, there are many choices to select from, with chemistry and your imagination serving as the only limits to what is possible through extrusion.
Send us your application specifications
Let Inplex demonstrate it’s color and flexibility extruding your version of perfection. Experience precision manufacturing with exceptional service and support.