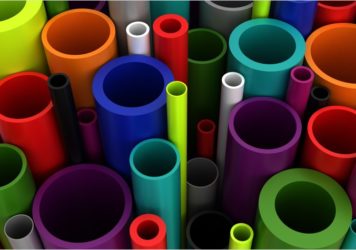
Custom Plastic Tubing
Inplex Custom Extruders has more than five decades of experience in providing custom plastic tubing solutions. Plastic tubing can be constructed out of a range of materials, spanning from flexible to semi-rigid to rigid. The options available for custom plastic tubing are greater than ever before. At Inplex Custom Extruders, we achieve this versatility by melting the plastic material and forcing it through a die before extruding it into the desired shape. The resulting product is then mechanically cut and finished according to each specific order, with a wide variety of sizes, shapes, and colors available. In addition, the coloring and opacity of the tubing can be customized according to your needs, affording more versatility in tubing applications.
Flexible Tubing
As the name suggests, flexible tubing offers the ability to bend according to your needs. There are seven different kinds of materials that can be used in the manufacturing of flexible tubing, including:
- Polyurethane
- Santoprene
- Flexible vinyl (FPVC)
- Low-density and linear low-density polyethylene (LDPE and LLDPE)
- Flexible nylon 11 and 12
Among these materials, PVC and polyurethane prove to be the most flexible, while nylon and polyethylene fall on the harder end of the plastic firmness spectrum. With that said, all are significantly more flexible than rigid tubing. Some general uses for flexible pasting tubing include utility (air and gas) and chemical lines, laboratory equipment, protective jacketing, water lines, and pump feeds. More flexible plastic tubing materials such as polyurethane and FPVC are also well-suited for being formed into pneumatic hose tubing, as they both show strong resistance to kinking.
Polyethylene
Perhaps the most commonly used plastic worldwide, polyethylene shines as a cost-effective tubing material. It finds wide use in applications that do not suffer from the lesser rigidity, at least when compared with PVC and polyurethane. Low-density polyethylene (LDPE) can be used in a wide range of temperature settings. It finds particularly notable use in food handling and the provision of drinking water.
Polyurethane
Distinguished by its excellent resistance to wear, polyurethane tubing also provides a good deal of flexibility and finds common use in applications involving liquids like fuel and oil.
FPVC
Flexible vinyl (FPVC) is strong, lightweight, resistant to abrasion, and approximately as flexible as rubber. As a result, it is a particularly versatile material that can be used in applications involving gases, liquids, or chemicals. Generally regarded as one of the most cost-effective materials available today, FPVC can be formed into unconventional shapes. As a result, it has found steady applications in home construction. However, applications that require additional toleration of pressure should rely instead on rigid vinyl (RPVC), which is less prone to kinking than FPVC.
Nylon
Nylon tubing finds notable use in robotics, manufacturing, and food processing applications thanks to its excellent resistance properties, whether to chemicals, impact, abrasions, or moisture. With a melting point of 256˚C/450˚F, nylon also sports a much higher level of heat resistance than most other plastic materials. It also finds use in large-scale hydraulic lines and the transportation of chemicals, oils, and fuels.
Semi-Rigid Tubing
Semi-rigid tubing combines strength and high abrasion resistance with a lightweight form. This, along with a high bend radius and low moisture absorption, makes it excellent for applications involving fluid transfer. Semi-rigid tubing can be made from:
- Polypropylene (PP)
- High-density polyethylene (HDPE).
Polypropylene
Polypropylene (PP) is a thermoplastic known for its lightness and dimensional stability. Sporting excellent electrical properties and surface hardness, PP finds common use in packaging and labeling applications. For example, most plastic hinges, including those on flip-top bottles and breath mint boxes, are made from polypropylene. Plastic containers are also commonly made out of polypropylene, as are other consumer products such as trash cans and plates.
High-Density Polyethylene
High-density polyethylene (HDPE) offers exceptional inertness among plastics. It naturally finds use in the food and beverage industry as well as in laboratory and chemical processing, where impermeability is necessary.
Rigid Tubing
The most durable grouping of materials available for custom plastic tubing, rigid tubing provides strength, sturdiness, and robustness in a variety of industrial applications. There are a number of different rigid plastic materials available to serve as options depending upon your exact needs. These include:
- Polycarbonate
- Rigid vinyl (RPVC)
- ABS
- High impact polystyrene (HIPS),
- Butyrate
- Propionate
- PETG
Of these options, polycarbonate and RPVC are the two most commonly used in tubing, although each material boasts some particularly notable uses for certain applications.
Polycarbonate
Polycarbonate is among the most common materials used for extruding, as it can be shaped into virtually any shape. It offers excellent temperature resistance and insulation properties. Some notable applications for polycarbonate tubing include medical devices, food chutes, LEDs, and sight glasses.
Rigid Vinyl
Rigid Vinyl (RPVC) offers excellent chemical resistance properties. Along with its superior rigidity and affordability, RPVC finds very common use in plastic tubing when high durability and pressure resistance is required, such as the plumbing and construction industries. However, the presence of chemical additives like lead and cadmium require that PVC be ordered at certified FDA grades to be considered safe for use with drinking water.
ABS
ABS finds special use in tubing used in drain-waste-vent pipe systems as well as in sewer systems and insulation for electrical cables.
High Impact Polystyrene
(HIPS) is used in a variety of industrial and commercial settings such as the food industry.
Butyrate and Propionate
These are transparent thermoplastics that find particular use in mailing, packaging, and storage applications.
PETG
PETG is used to create plastic packaging tubes of varying thicknesses. Industries, where PETG tubing is used, include robotics, electronics, and consumer goods such as containers and water bottles.
Inplex Custom Extruders, LLC
At Inplex, we are experienced in providing custom plastic tubing solutions. Orders can be cut to length, split full length, wound on spools or coils, fabricated in-line, finished according to your exact specifications. We offer a wide range of stock and custom colors are in addition to various opacities, from transparent to translucent to fully opaque.
If you are in need of a custom extrusion order, please request a quote today and let us know about the custom plastic tubing that you require.
Back to Blog