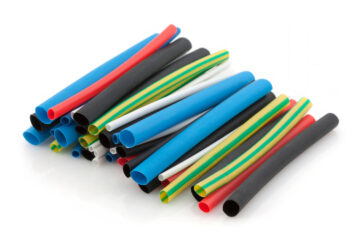
How Inplex Helps Clients Meet Goals Through Material Selection
In custom plastic extrusion, choosing the right material is one of the most critical steps toward ensuring product performance, durability, and cost-effectiveness. At Inplex, material selection is not just a technical decision—it’s a strategic partnership with clients to meet their unique goals, whether those involve strength, flexibility, environmental sustainability, or budget constraints.
By leveraging deep industry expertise and advanced material knowledge, Inplex helps clients navigate the complex landscape of plastics to deliver optimized solutions tailored to their specific applications. Let’s take a look at some specific examples of professional material selection.
Understanding Client Goals
Every client comes with distinct project requirements. Some prioritize mechanical strength and longevity for demanding industrial environments. Others need materials that offer flexibility, UV resistance, or chemical compatibility.
Still, some focus primarily on sustainability, seeking recycled or bio-based options. Inplex starts by thoroughly understanding these goals and constraints, ensuring the material chosen aligns perfectly with the intended function and operating conditions.
Comprehensive Material Expertise
Inplex’s team brings extensive knowledge of a wide range of thermoplastics, including polyethylene (PE), polypropylene (PP), polyvinyl chloride (PVC), and engineering plastics such as nylon and acrylic. This expertise allows Inplex to evaluate the advantages and limitations of each material type against client needs.
For instance, if a client requires a weather-resistant outdoor profile, Inplex might recommend a UV-stabilized PVC or a specially formulated polyethylene that withstands sun exposure and temperature fluctuations. For applications demanding high impact resistance or chemical durability, nylon or reinforced composites could be better fits.
Customizing Formulations for Performance and Cost
Material selection is rarely a one-size-fits-all decision. Inplex works closely with suppliers and uses custom compounding when necessary to tweak material properties—such as adding fillers for strength, plasticizers for flexibility, or colorants for aesthetics. This tailored approach balances performance and cost, helping clients avoid over-engineering while ensuring their products exceed expectations.
Balancing Sustainability and Functionality
Sustainability is an increasingly important factor in material selection. Inplex helps clients explore recycled plastics, post-industrial resins, and bio-based polymers where feasible. The challenge lies in meeting environmental goals without compromising product integrity. Inplex’s expertise ensures recycled or sustainable materials are incorporated in a way that maintains quality, durability, and regulatory compliance.
Material Testing and Validation
To guarantee that the chosen material meets all specifications, Inplex employs rigorous testing protocols. This includes analyzing mechanical properties, chemical resistance, and dimensional stability. Material testing minimizes risks, ensures regulatory compliance, and verifies that the extrusion process will consistently produce high-quality parts.
Collaborative Problem Solving
Inplex values collaboration throughout the product development cycle. From initial material selection to prototyping and production, Inplex’s technical team works hand-in-hand with clients to troubleshoot issues and optimize material choices. This partnership approach accelerates time-to-market and helps clients adapt quickly to evolving needs or industry trends.
Custom Extrusion with Inplex
Looking for quality custom extrusion products and services? Inplex is one of the leading custom extrusion services in the US and has almost 60 years of experience. We pride ourselves on our ability to put the right talent and technology in place to perform the best possible job for our clients.
We own a 42,000 sq. ft. facility in Naperville, Illinois, that is temperature-controlled and features an environmentally friendly closed-loop water cooling system. If you have specific needs or questions, don’t hesitate to contact us!
Back to Blog