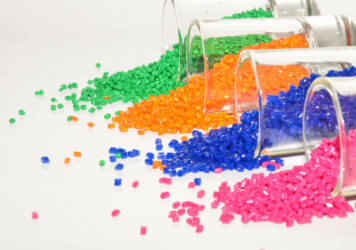
How Plastic Extrusion is Revolutionizing the Consumer Goods Market
The consumer goods market is one of the most dynamic and rapidly evolving industries, driven by consumer demand for innovative products, cost-effective solutions, and sustainable alternatives. Among the many manufacturing processes that have played a crucial role in shaping the modern consumer goods landscape, plastic extrusion stands out for its versatility, efficiency, and ability to produce high-quality products at scale.
Plastic extrusion is revolutionizing the consumer goods market by enabling manufacturers to create custom products that meet the diverse needs of consumers while also supporting sustainability efforts and improving product performance. Let’s take a closer look.
Creating Custom Products for Diverse Consumer Needs
One of the primary reasons plastic extrusion is revolutionizing the consumer goods market is its ability to create custom, highly specialized products. Whether it’s packaging, home goods, or personal care items, plastic extrusion allows manufacturers to design products with unique shapes, sizes, and material properties that meet specific consumer demands.
In the consumer electronics market, plastic extrusion plays a critical role in producing various components such as cable insulation, connectors, and protective casings for gadgets. The precision of the extrusion process ensures that these components fit perfectly within the product’s design and provide the necessary protection and performance required by consumers. As technology advances, the demand for custom, high-performance components has grown, and plastic extrusion is uniquely equipped to meet these needs.
Improving Product Durability and Functionality
Plastic extrusion is not only about creating aesthetically pleasing products; it also offers significant benefits in terms of product durability and functionality. For example, in the automotive industry, plastic extrusion is used to produce a wide range of consumer goods, including interior components, trim pieces, and seals. These parts are made from durable, lightweight plastic materials that offer resistance to wear, corrosion, and temperature fluctuations, ensuring that the products last longer and perform better under various conditions.
Moreover, the ability to create multi-layered plastic products through extrusion allows manufacturers to integrate different properties into a single product. For instance, an extruded plastic product can have a layer that is UV-resistant for outdoor use, a layer that provides insulation for energy efficiency, and a layer that is aesthetically pleasing for consumer appeal. This level of customization and performance enhancement would be difficult or cost-prohibitive with other manufacturing methods.
Supporting Sustainability Efforts in Consumer Goods
Sustainability is an increasingly important concern for both consumers and manufacturers in the consumer goods market. Plastic extrusion has become a key player in promoting eco-friendly practices by enabling the production of recyclable products and reducing waste. Many consumer goods manufacturers are turning to recycled plastics for their extrusion processes, which helps reduce the environmental impact of production and promotes a circular economy.
For example, extruded products such as packaging can be made from recycled plastic materials, which reduces the need for virgin plastic and conserves natural resources. Additionally, because plastic extrusion can be a highly efficient process with minimal waste, it supports the creation of products that are not only sustainable but also cost-effective. The ability to use biodegradable and environmentally friendly plastics in extrusion further supports the growing demand for eco-conscious consumer goods.
Custom Extrusion with Inplex
Looking for quality custom extrusion products and services? Inplex is one of the leading custom extrusion services in the US, with over 50 years of experience. We pride ourselves on our ability to put the right talent and technology in place to perform the best possible job for our clients.
We own a 42,000 sq. ft. facility in Naperville, Illinois, that is temperature-controlled and features an environmentally friendly closed-loop water cooling system. If you have specific needs or questions, don’t hesitate to contact us!
Back to Blog