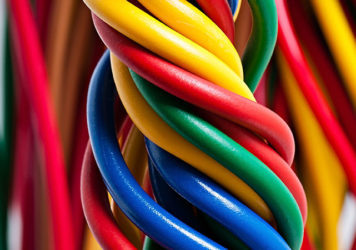
Plastic Coating and Jacketing
Plastic coating can enhance the use of virtually any metal, including steel, aluminum, copper, bronze, brass, nickel, and alloys. These coatings offer a number of benefits within both industrial and commercial contexts and can be customized for any metal wires, bars, or tubing. Plastic coating can increase the usefulness and lifespan of tools and materials made from almost any metal. These coatings are typically applied through an industrial hot-dip coating technique or sprayed directly onto a metal surface. Almost every industry can benefit from custom extruded plastic jacketing, whether it’s for in-house machinery or consumer use.
A few ways that Metal Parts can Benefit from Plastic Jacketing:
Moisture-Proofing
The plastic coating creates a barrier to water when applied to metal, decreasing corrosive damage and rust. It also adds a layer of safety in applications where electricity is conducted.
Appearance
Multi-colored plastics make it easier for workers and consumers to identify metal wires, tubing, and bars on sight. This makes the organization simpler, and public-facing consumer products more visually attractive.
Sterilization
Plastic-coated tools can be much more thoroughly cleaned and sterilized, making it an ideal solution for industrial applications.
Temperature Resistance
Industrial and commercial applications for metal tubing and bars often require metal parts to maintain stable temperatures. Plastic coatings help minimize heat conduction and keep metal safe to touch.
Chemical Resistance
Scientific processes that involve chemical use can negatively impact the useful lifespan of metal tools and materials. Plastic coating adds chemical resistance that extends the life of scientific tools.
Types of Plastic-Coated Wire
Plastic coated wire is used to create materials and products that can stand up to weather extremes, excessive moisture, and frequent use. Coated wire has all the same benefits as standard, high-quality wire, with the added bonuses of safety and ease of use. Applications for plastic coated wire include:
- Construction tools, equipment, and materials
- Aircraft engineering and maintenance
- Consumer DIY and craft projects
- Exercise equipment
- Stage rigging
- Municipal bridge construction
Plastic wire jacketing can also enhance communications devices, chain-link fencing, and electrical insulation.
Types of Plastic-Coated Tubing
The primary function of plastic-coated metal tubing is to conduct liquids and gases in industrial or commercial contexts. By coating these metal pieces in plastic jacketing, they become safer to handle, easier to clean, and longer-lasting. A few applications for plastic-coated metal tubing include:
- Oil rigs
- Automobile parts
- Water and gas supply systems
- Sewage and drainage operations
- Irrigation systems
The firefighting field has benefitted from plastic-coated tubing, as well. Plastic jackets allow the flexible tubing used by firefighters to be handled even under extreme temperatures. They also allow equipment that comes in contact with a great deal of water to remain corrosion and rust-free, extending its life.
Types of Plastic-Coated Metal Bars
Plastic coated metal bars are an ideal solution for both industrial machinery and public-facing consumer products. Metal bars offer strength and reliability to a structure or piece of machinery, while plastic coating helps prevent injuries and makes the product more visually appealing to consumers.
Common uses for plastic-coated metal bars include:
- Playground equipment
- Street drainage systems
- Public fountains
- Architectural fencing
- Machine guarding
- Water traps
Plastic coating also adds protection from the elements, which is especially useful in municipal projects, where cost and longevity are key considerations. This provides added value for the community and responsible use of tax dollars. The added protection to the metal in water systems also helps prevent corrosion and the leaching of byproducts into public water supplies. The relatively simple process of plastic jacketing can result in significant long-term savings for your business or community. Plastic coated metals last longer and can withstand harsh conditions which are easier for workers and consumers to handle. Materials that conduct electricity and heat can be made safer and simpler, without compromising quality. With custom extruded plastic coating, you can find the right jacketing solution for your metal wiring, bars, and tubing needs.