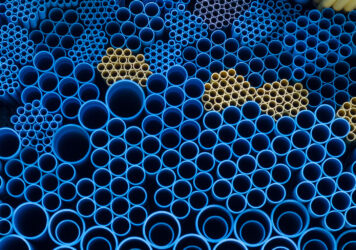
The Benefits of Using Custom Plastic Extrusion for Your Projects
Custom plastic extrusion offers numerous benefits, including cost savings, design flexibility, durability, and sustainability. Whether you’re developing a new product or optimizing an existing one, this manufacturing process provides reliable and high-quality solutions for a diverse range of industries.
By leveraging this, businesses can achieve high precision, cost efficiency, and enhanced performance in their products. Here are some key benefits of using custom plastic extrusion for your projects. Let’s take a closer look.
Design Flexibility
One of the primary advantages of custom plastic extrusion is the ability to create complex and unique profiles that meet specific design requirements. Whether you need intricate shapes, hollow sections, or reinforced structures, extrusion allows for high customization without sacrificing strength or durability.
Cost-Effective Production
Custom plastic extrusion is a cost-efficient manufacturing method, especially for large production runs. The continuous process minimizes material waste, optimizes production speeds, and reduces labor costs, making it an economical choice for businesses looking to scale their operations.
Wide Range of Material Options
The extrusion process supports a variety of thermoplastics, including PVC, polyethylene, polypropylene, and ABS. Each material offers distinct properties such as flexibility, impact resistance, and chemical stability, ensuring that your project benefits from the most suitable material selection.
Consistent Quality and Precision
With advanced extrusion techniques, manufacturers can achieve high precision and uniformity in their products. State-of-the-art dies and quality control measures ensure that each extruded profile meets exact specifications, resulting in reliable and consistent performance.
Strength and Durability
Custom extruded plastic components are designed to withstand various environmental conditions, including extreme temperatures, UV exposure, and chemical exposure. With the addition of reinforcements and protective coatings, these components can offer superior strength and longevity.
Lightweight and Versatile
Compared to traditional materials like metal and wood, plastic extrusion provides lightweight yet sturdy solutions for a variety of applications. This makes it an ideal choice for industries where weight reduction is crucial, such as automotive and aerospace.
Sustainable and Environmentally Friendly
Many plastic extrusion processes incorporate recycled materials and generate minimal waste, making them more sustainable than other manufacturing methods. Additionally, extruded plastic components can often be recycled at the end of their lifecycle, contributing to a circular economy.
Rapid Prototyping and Customization
For businesses looking to develop prototypes or modify existing designs, custom plastic extrusion offers a fast and efficient solution. Quick adjustments to die designs and material compositions enable manufacturers to produce prototypes and customized products with minimal downtime.
Custom Extrusion with Inplex
Looking for quality custom extrusion products and services? Inplex is one of the leading custom extrusion services in the US, with over 50 years of experience. We pride ourselves on our ability to put the right talent and technology in place to perform the best possible job for our clients.
We own a 42,000 sq. ft. facility in Naperville, Illinois, that is temperature-controlled and features an environmentally friendly closed-loop water cooling system. If you have specific needs or questions, don’t hesitate to contact us!
Back to Blog