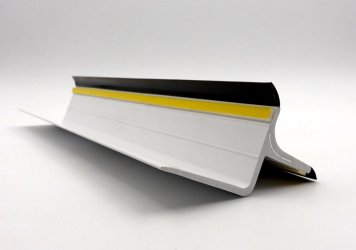
Co-extrusion Vs. Tri-extrusion Plastic Tubing & Profiling
At Inplex, we take pride in our ability to adapt to our customers’ exact specifications for custom plastic extrusion. We have a history of fulfilling orders with exceptional service and precision. Let us know what length, color, and rigidity you are looking to manufacture and we’ll come up with the perfect solution to meet your specifications.
Inplex uses co-extrusion to manufacture plastic tubing and plastic profiles according to customer specifications, with the ability to incorporate different colors and hardness into a single continuous part. Inplex plastic tubing, plastic profiles, and plastic coating can all be custom ordered by length, color, rigidity, and material.
What is Custom Plastic Extrusion?
The word “extrude” is made up of two components that have Latin roots, the word extrusion literally means “to push out,” referring to the fact that the raw material is “pushed out” through the extruder into the desired shape.
Plastic extrusion is the process by which material is pushed through a die to create an object of a fixed cross-sectional profile. Plastics are melted and formed into a profile through a continuous extrusion process that feeds raw plastic through the barrel of an extruder, where it is heated and later cooled to harden once it has taken on its desired shape. Common objects created through plastic extrusion include pipes, tubes, fencing, and thermoplastic coating.
What is Custom Co-extrusion?
Co-extrusion is the simultaneous extrusion of two layers of material through the operation of multiple thermoplastic melt streams. In co-extrusion, two different extruders work to melt and push different plastics through a single die, which then extrudes the materials into the desired shape. Co-extrusion can control layer thickness by adjusting the relative speeds and sizes of the extruders in operation.
Custom co-extrusion is highly useful because it can allow blended materials to undergo extrusion into a single object while keeping them separated into different layers. This grants substantially enhanced versatility in terms of strength, stiffness, wear resistance, and oxygen permeability. It also allows the production of objects with a wide variety of colors, finishes, and rigidities.
Plastic co-extrusion is often used to create plastic substitutes for conventional wood products, such as fences and decks. Thanks to the versatility of plastics that have undergone the co-extrusion process, it is possible to visually mimic wood while still producing a cost-effective and weather-resistant final product.
What is Tri-extrusion?
Custom tri-extrusion offers all of the same features and benefits of co-extrusion while handling three different materials in the same extrusion process. While each material is usually fed through a separate extruder, it is possible to make a single extruder supply two or more plastic materials at once. A range of materials of varying rigidities can safely go through either the co-extrusion or tri-extrusion processes. In order of ascending rigidity, these materials include:
Flexible: Polyurethane, Santoprene, flexible vinyl (FPVC), low-density and linear low-density polyethylene (LDPE and LLDPE), and flexible nylon 11 and 12.
Semi-Rigid: Polypropylene (PP) and high-density polyethylene (HDPE).
Rigid: Polycarbonate, rigid vinyl (RPVC), acrylonitrile butadiene styrene (ABS), high impact polystyrene (HIPS), butyrate, propionate, and polyethylene terephthalate (PETG).
Applications of Custom Plastic Extrusion
In the expansive landscape of manufacturing and product development, custom plastic extrusion emerges as a pivotal technique with wide-ranging applications across diverse industries like highway safety, agriculture, consumer housewares, outdoor living, and so much more. This versatile process involves shaping raw plastic materials into distinct profiles, presenting opportunities for innovation in each of these sectors.
Using Co-extrusion for Custom Plastic Tubing
Co-extrusion has found a reliable application in the production of tubing, with the multi-colored drinking straw serving as an excellent example of how co-extrusion can create a visually appealing and structurally sturdy product. Similar striped tubing is also used in the medical field, where the various colors of stripes often denote its intended use or contents.
Quality Tri-extrusion for Various Industries
Custom tri-extrusion is particularly vital in the medical field, where many medical devices simply cannot be produced without the use of multiple raw materials. Medical devices that make use of tri-extrusion include catheter systems, dialysis equipment, stents, and coronary implant delivery systems.
Inplex Custom Plastic Extruders, A Leading Custom Plastic Extrusion Manufacturer
Inplex conveniently manufactures both profiling and tubing, which means you won’t have to go to more than one place to completely satisfy your tubing and profiling needs. Whether you need samples or have a tight deadline and need concentrated assistance as quickly as possible, Inplex looks forward to building a strong business relationship and helping you to achieve your custom extrusion goals.